Nous entendons souvent dire « nous portons des vêtements, les chaussures nous portent ».
La chaussure est un produit technique, compliqué à fabriquer. Elle doit répondre à des contraintes de podologie, d’usure et d’esthétique.
Nous l’évoquions dans un précédent article, il reste des usines de production de chaussures en France.
Depuis plusieurs années, l’équipe SCF (société choletaise de fabrication) assiste à des visites d’usines de fabrication de chaussures avec l’AFTIC.
Ceci nous a permis d’observer la fabrication des chaussures.
Il est temps de vous en dire plus sur la production d’une paire de chaussure.
Il s’agit d’aborder les diverses techniques de fabrication de chaussures et le processus de fabrication, étape après étape.
Les diverses techniques de fabrication de chaussures
Chaussures injectées, chaussures soudées, chaussures cousues … et quelle couture ? Cousu Blake, cousu Goodyear, cousu norvégien, …
C’est à en perdre son latin !
Tentons d’y voir plus clair sur les diverses techniques de fabrication de chaussures.
Les chaussures cousues
C’est la manière traditionnelle de fabriquer des chaussures. Les derbies, richelieu et mocassins sont souvent cousus, même si d’autres méthodes sont de plus en plus appliquées comme l’injecté ou le soudé.
Souvent les chaussures haut de gamme sont cousues.
Dans cette méthode, la tige et la semelle sont cousues ensemble. Plusieurs façons de coudre existent :
- Blake, c’est un montage élégant et souple. Une seule couture visible à l’intérieur de la chaussure au niveau de la semelle traverse toutes les couches pour lier la tige à la semelle.
- Goodyear est considéré comme la plus robuste, durable et prestigieuse des coutures. Une bande de cuir nommée trépointe est ajoutée entre la tige et la semelle. Ce mode de fabrication est souvent appliqué à des chaussures chères, durables et réparables. C’est une couture latérale, visible. Souvent les techniciens disent « coudre dans le mur » !
- Un dérivé de la couture Goodyear est la coutre Norvégienne. Il s’agit d’une double couture visible. Cependant, l’assemblage nécessite trois coutures dont deux sont visibles ! La tige et première de montage sont cousues puis la trépointe est cousue à la tige. Enfin, la semelle extérieure est cousue.
- Sandalette ou Kneipp est une construction flexible avec une couture qui relie la tige à une semelle intermédiaire ou à une première de propreté. Ce n’est pas très solide ni étanche.
Nous vous expliquons plus en détails le processus de fabrication de la chaussure dans nos chapitres suivants.
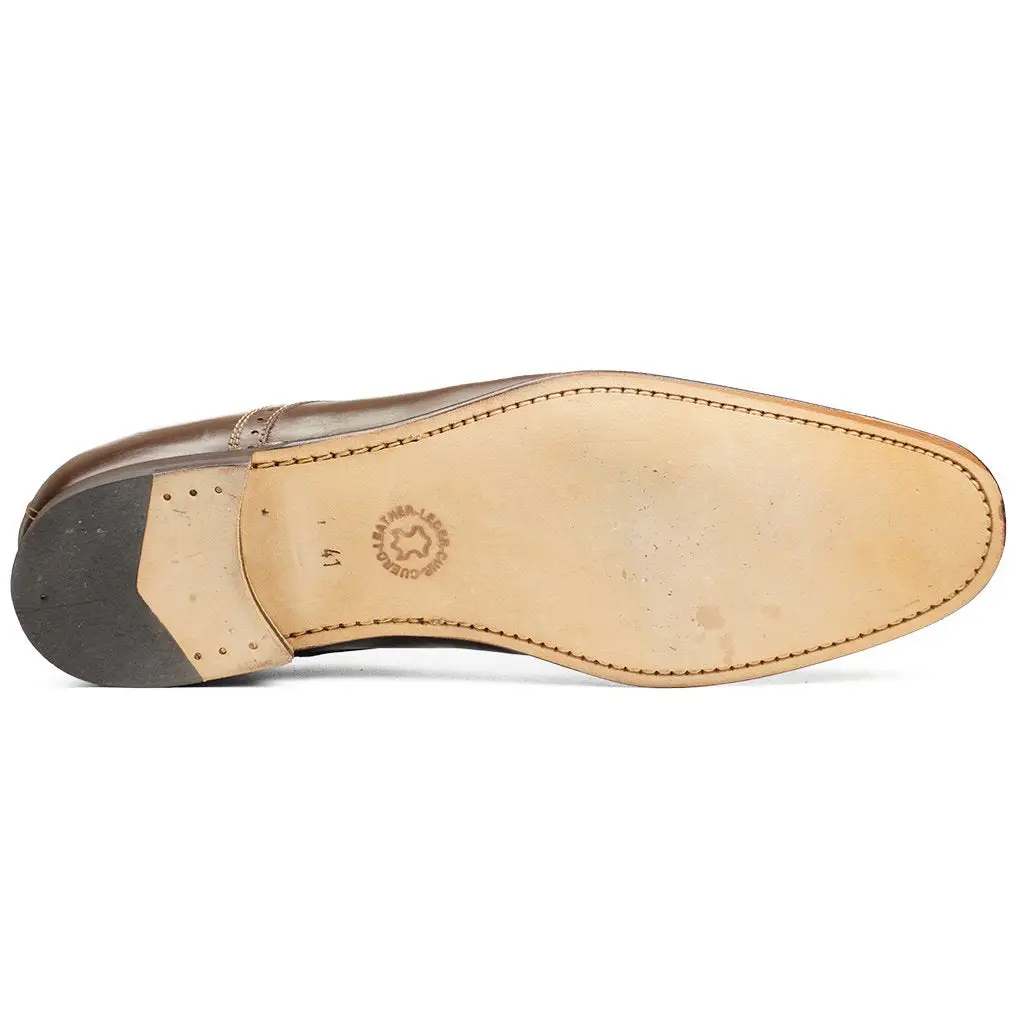
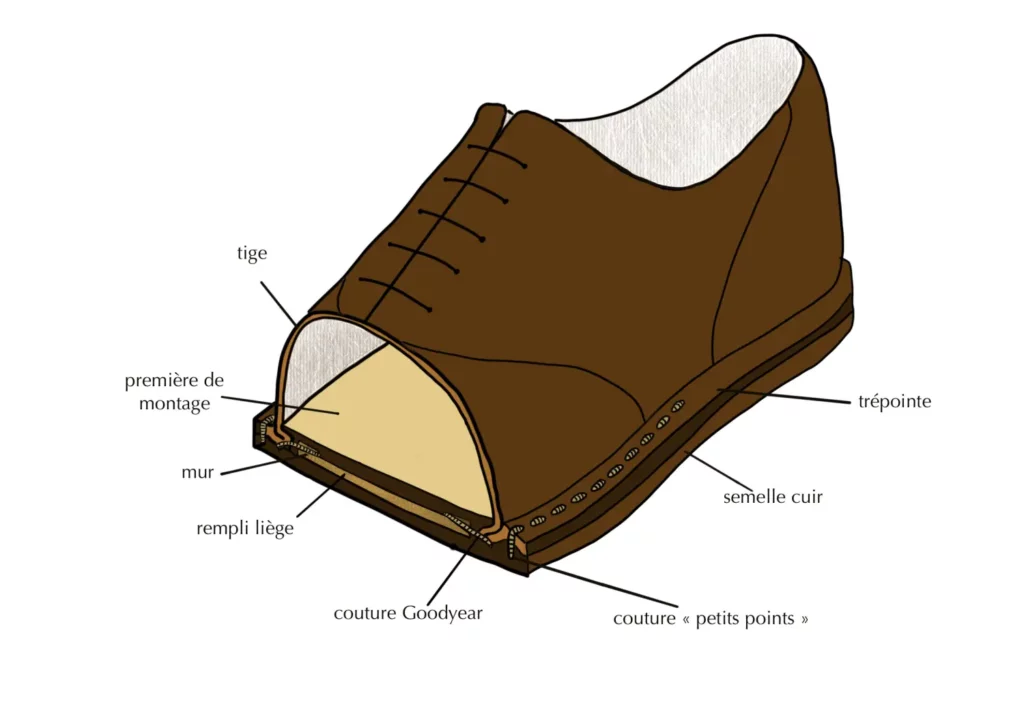
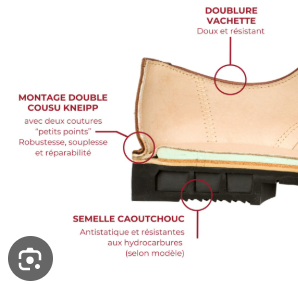
Le soudé ou le collage
La semelle est fixée à la tige par collage. Depuis l’émergence des sneakers et tennis, c’est la technique la plus utilisée.
Ainsi, il y a absence de couture visible entre la tige et la semelle extérieure.
Inconvénient de cette technique : une durée de vie souvent plus limitée et une impossibilité de ressemelage dans la plupart des cas.
Cependant, depuis quelques années, des chaussures soudées sont conçues pour être démontées et donc réparables.
La chaussure vulcanisée
Le vulcanisé consiste à granuler la semelle en gomme latex. Puis cette semelle est moulée sur la tige par vulcanisation.
La vulcanisation est une réaction chimique qui lie le caoutchouc de manière permanente à la tige, souvent en toile ou en cuir.
La vulcanisation est une méthode de fabrication éprouvée qui confère aux chaussures des qualités uniques de robustesse, de flexibilité et d’adhérence. Ainsi, ces chaussures sont beaucoup utilisées pour un usage quotidien et pour certaines activités sportives.
L’injection ou la fabrication automatisée
Des granulées de PVC sont injectés dans un moule pour former le dessous de la chaussure.
La semelle est directement injectée sur la tige. Ainsi, la chaussure injectée est souvent assemblée en une seule fois.
Cette technique est largement utilisée pour les chaussures de sécurité, certaines chaussures de sport, des bottes, et même des chaussures de ville pour leurs propriétés d’étanchéité, de légèreté et de confort.
Cette technique permet d’obtenir des chaussures performantes en termes d’étanchéité, de durabilité et de confort, particulièrement adaptés aux environnements exigeants.
Beaucoup de productions de chaussures injectées sont automatisées.
Le processus de fabrication de chaussures
La fabrication d’une chaussure implique la succession de 14 étapes de la création à la mise en boite. Ces étapes diffèrent dans leur contenu selon la technique de fabrication de chaussure. En effet, selon que la chaussure soit cousue, soudée ou injectée, le contenu des étapes est différent.
Etape 1 – La création d’une nouvelle paire de chaussure
La première étape consiste à s’inspirer et à observer les tendances.
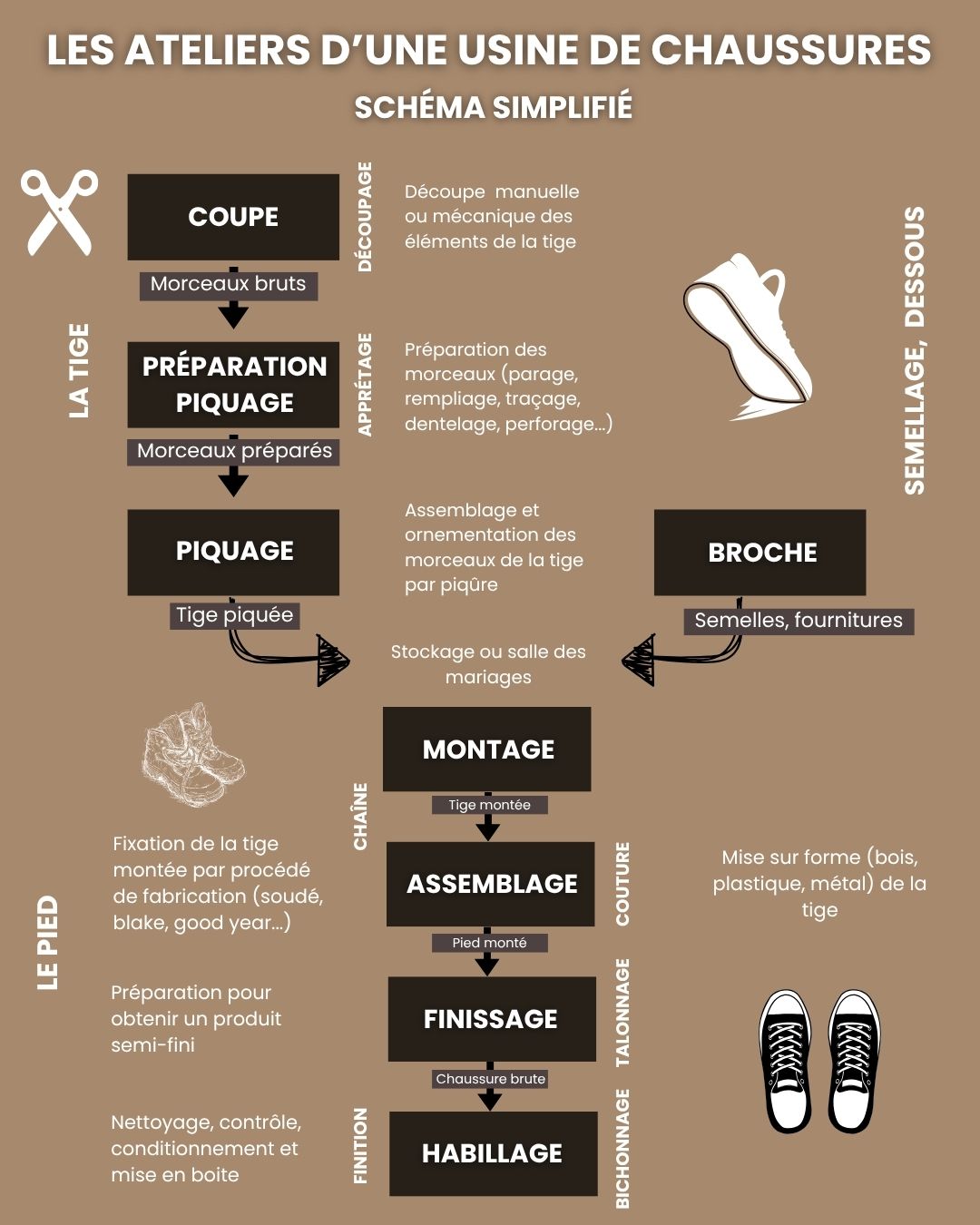
Des stylistes ou chefs de produits vont consulter des agences de tendances, des revues, leurs archives et l’observation de la rue pour imaginer un nouveau modèle.
Le styliste choisit aussi la couleur ou les couleurs de la chaussure.
Il s’agit d’un travail créatif suscitant l’imagination et l’inspiration de la part du styliste.
Puis, le styliste va dessiner de nombreuses esquisses et ébauches. Peu sont gardées !
Souvent des logiciels sont utilisés pour réaliser en dessins 3D les modèles.
Pour donner forme aux premiers modèles, plusieurs dessins sont traduits en maquettes. De plus en plus, l’impression 3D est utilisée.
A la suite de cette étape, souvent un seul modèle est retenu.
Etape 2 – La modélisation et la fabrication de la forme
Les formes représentent la forme intérieure de la chaussure.
Dans le passé, des menuisiers ou formiers fabriquaient en bois ces formes. Les bottiers haut de gamme continuent de les fabriquer en bois. Ainsi, lors de la création d’une chaussure sur mesure, la forme est fabriquée que pour ce modèle. Pour ces bottiers, le nom du client est alors indiqué sur la forme.
De nos jours, les formes sont fabriquées par injections plastiques. Ainsi, les formes sont en plastiques.
Il existe aussi des formes fabriquées en impression 3D.
Pour chaque pointure d’une chaussure (ou demi-pointure dans le haut de gamme), une forme est créée.
Puis, les lignes du modèle de chaussures sont reportées à plat pour obtenir le patron de la chaussure.
Il est utilisé des logiciels de CAO (Conception Assistée par Ordinateur). Il est par exemple utilisé Romans CAD, Shoemaster ou encore ICad3D.
Les talons et semelles sont aussi créés.
✏️ A noter : le métier de formier est technique, il s’agit de rendre la chaussure confortable à la morphologie du pied.
Etape 3 – Le patronage
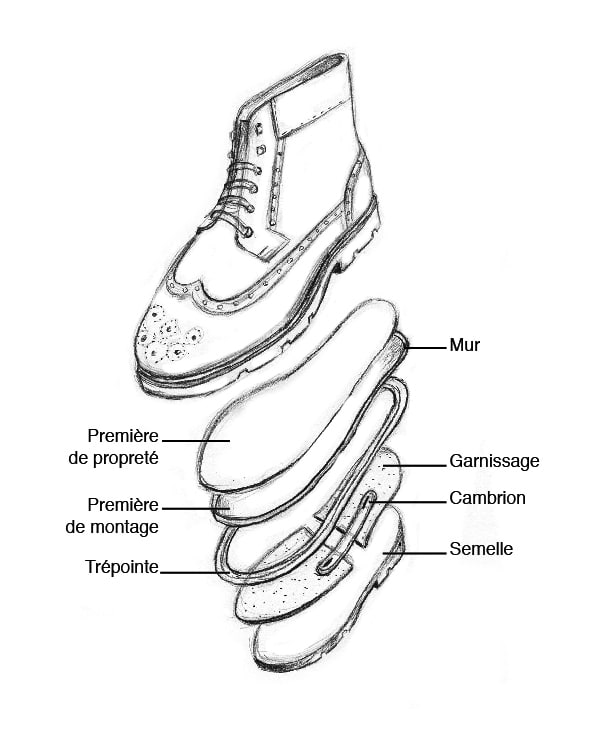
Le technicien expert de cette étape se nomme patronier ou modéliste (comme pour le textile).
Pour toutes les chaussures, le patron dessine des différentes pièces de la tige.
La tige est la partie du dessus de la chaussure. Cette tige peut être en diverses matières. Elle est en cuir pour les chaussures classiques et en toile pour les chaussures de type sneakers ou basquets.
Ces dessins vont permettre de créer les nomenclatures pour la fabrication industrielle.
✏️ A noter : que souvent la tige est doublée, il faut donc dessiner la partie extérieure et visible et la partie intérieure au contact avec le pied.
Là aussi, des logiciels peuvent être utilisés.
Etape 4 – La découpe des divers éléments de la tige
C’est la première étape de fabrication impliquant l’atelier. Ici commence les étapes où la chaussure va prendre sa forme.
Comme évoqué avant, la tige peut être en diverses matières : en cuir (chaussures traditionnelles), en toile (chaussures de ville de type sneakers), en matières techniques (chaussures de sport avec des PU et PVC) ou encore en tricot.
Nous voyons aussi arriver de nouvelles matières, éco-responsables, comme le Piñatex (cuir d’ananas), le cuir de pomme ou de raison, …
Il s’agit de découper chacune des pièces qui va constituer la tige dans les matières.
Il existe plusieurs façons de découper ces matières :
- A l’emporte-pièce : la manière traditionnelle est encore beaucoup utilisée pour des productions importantes. Des presses sont utilisées pour découper des matelas de tissus ou cuir. Cependant, des productions traditionnelles utilisent encore le tranchet pour découper les pièces unes à unes.
- Au laser ou jet d’eau avec l’utilisation d’une table de découpe et d’un logiciel. Pour information, le cuir se découpe au jet d’eau ou au couteau mais pas au laser.
Outre la nécessité de découper chacune des pièces à la mesure exacte, l’enjeu est de détecter sur la matière les défauts. De plus, il faut aussi optimiser la découpe dans une surface pour éviter les pertes de matière.
De nouveau, des logiciels sont utilisés pour aider l’opérateur à placer les pièces à découper.
Etapes 5 et 6 – La préparation et le piquage pour assembler la tige
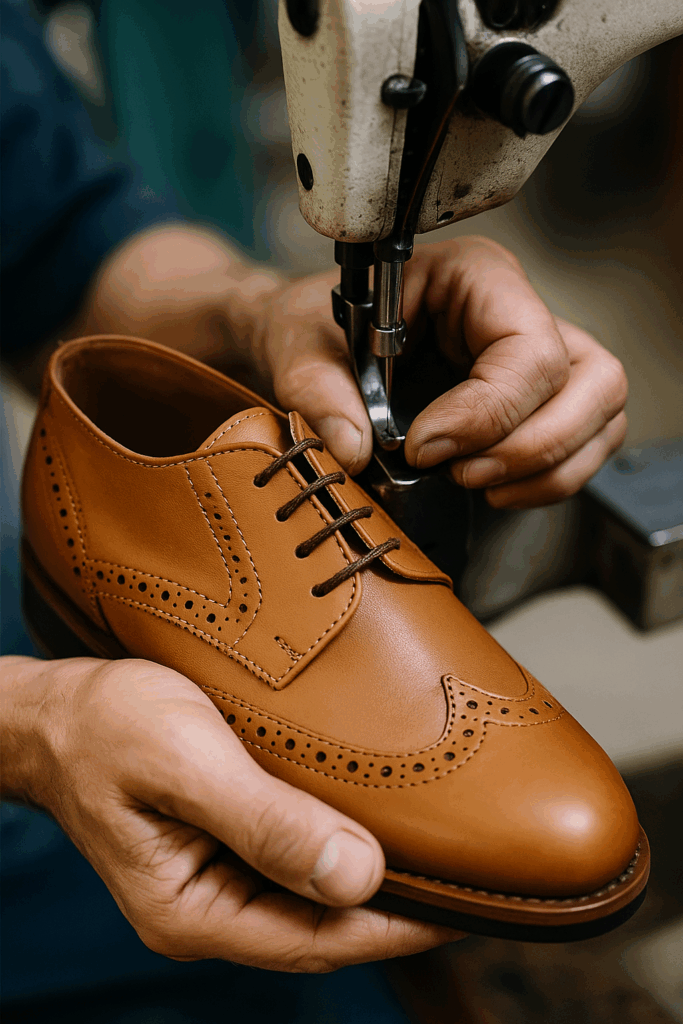
Ce sont deux étapes : la préparation et le piquage.
Ces étapes de production sont souvent la plus longues et coûteuses. Peu d’usine réalisent encore leurs tiges en France, sauf dans le haut de gamme.
Toutes les pièces de la tige de la chaussure vont être préparées par des actions aux noms de parage, de rempliage, de perforage, etc.
Puis, ces pièces sont assemblées par couture. Le piquage est une opération technique. Elle consiste à assembler les pièces ensemble pour former la tige. Cet assemblage peut être aussi décoratif, à l’image d’une broderie.
✏️ A noter : le développement de tige en tricot. Ces tiges évitent l’étape de découpe et de piquage. Le tricot est directement fabriquer en prenant la forme du dessus de la chaussure. Il existe aussi des techniques de thermoformage de la tige.
✏️ A noter : Notre partenaire SCF fournit des petits cordons, blancs ou de couleurs, qui servent à tenir en position la tige. Ce cordon est enfilé dans les emplacements des lacets.
- SCF fournit aussi les tire-bottes (boots et bottes) et autres bordures (ballerines).
Etape 7 – Préparation de la broche
C’est à cette étape que la fabrication de la partie de dessous de la chaussure débute. Le pied ou le dessous est donc le pendant de la partie de dessus de la chaussure aussi nommée la tige.
Il s’agit de préparer les semelles, les premières de montage, les talons, …
Des gabarits et des formes sont utilisés ; ceux fabriqués à l’étape 2.
Etapes 8 et 9 – La salle de mariage et le montage
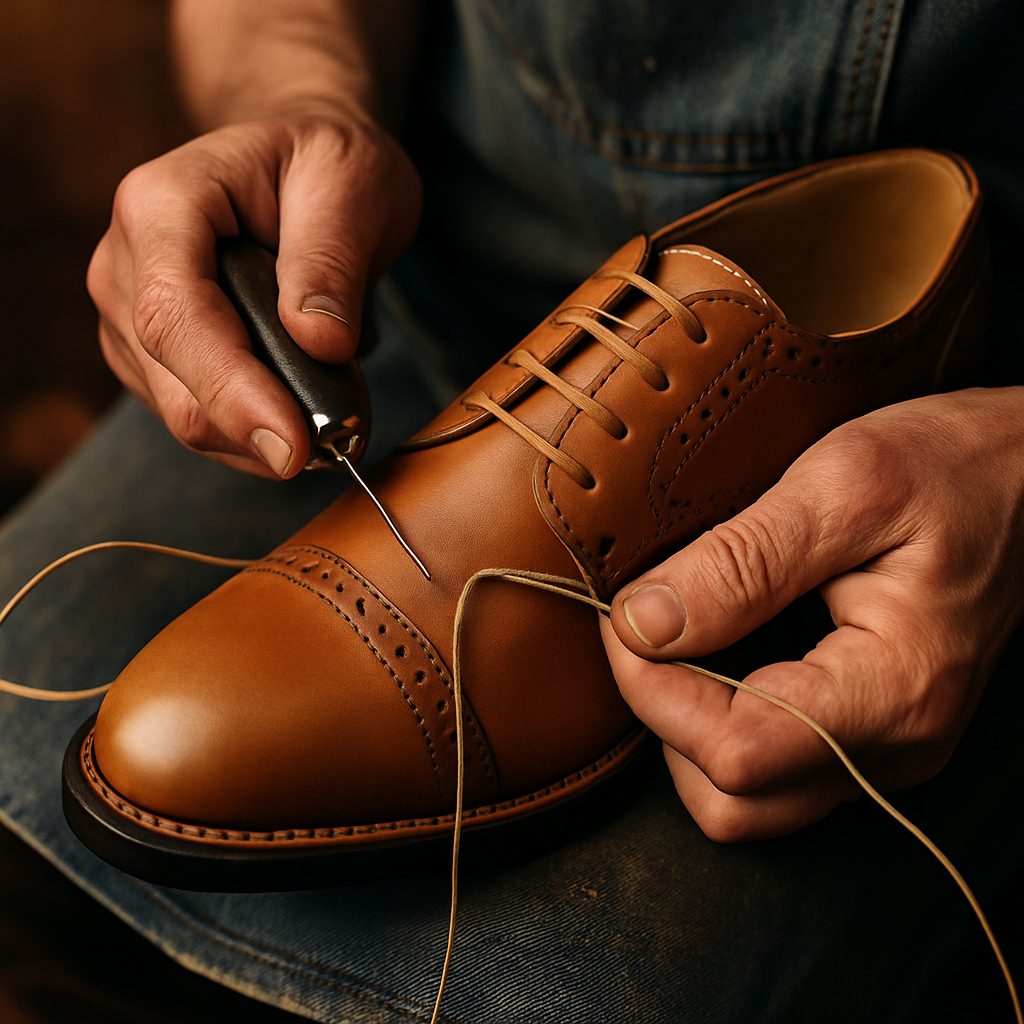
Il s’agit-là aussi de deux étapes.
Pour la salle de mariage (quel beau nom !), la forme, la tige, la première de montage et la semelle sont rassemblées par paire et par pointure.
Puis, lors du montage, la première de montage, clé de voute de la chaussure, est positionnée sur la forme.
La tige est plaquée sur forme et l’excédent de matière est rabattu sur la première de montage par collage.
Selon la méthode de fabrication, la semelle peut être collée, cousue (comme le cousu Blake ou Goodyear), ou même injectée directement sur la tige (voir le premier chapitre de ce texte).
Cet assemblage est mécanisé. Selon la méthode de fabrication, la machine est différente. Cependant, ce sont généralement pour cette étape des machines impressionnantes.
✏️ A noter : Sigier Capelle, entreprise du nord, fabrique les fils de couture des chaussures pour les cousus Black, Norvégien ou Goodyear.
Ce sont des fils techniques et particuliers.
Etapes 10, 11 et 12 – L’encollage, l’affichage et le soudage
Lors de l’encollage, le dessous de la chaussure et la semelle sont préalablement encollés.
Puis, la semelle est positionnée sur le dessous de la chaussure.
Enfin, la semelle est “soudée” à la première (de montage) et la tige. Ainsi la semelle est fixée par une forte pression exercée par-dessus, c’est une opération mécanisée.
Cette étape est différente selon la méthode de fabrication.
Ainsi, pour le montage collé ou soudé, il y a thermoformage. La chaussure montée sur forme est souvent passée dans des fours ou sous des lampes pour que le matériau de la tige épouse parfaitement la forme et pour que les renforts (bout dur, contrefort) durcissent et donnent de la tenue à la chaussure.
Pour les chaussures cousues, il y a selon la technique de couture (Blake, Goodyear, Norvégien ou Sandale) une ou plusieurs coutures.
Etape 13 – La talonnage
Le talon est fixé sur la chaussure, sous la semelle, avec des pointes et souvent de la colle.
Cette opération est mécanisée pour la chaussure femme et souvent manuelle pour les chaussures classiques.
Il n’y a souvent pas cette étape pour les chaussures collées ou injectées. La partie de dessous de la chaussure constitue un ensemble unique incluant déjà le talon.
Etape 14 – Le bichonnage
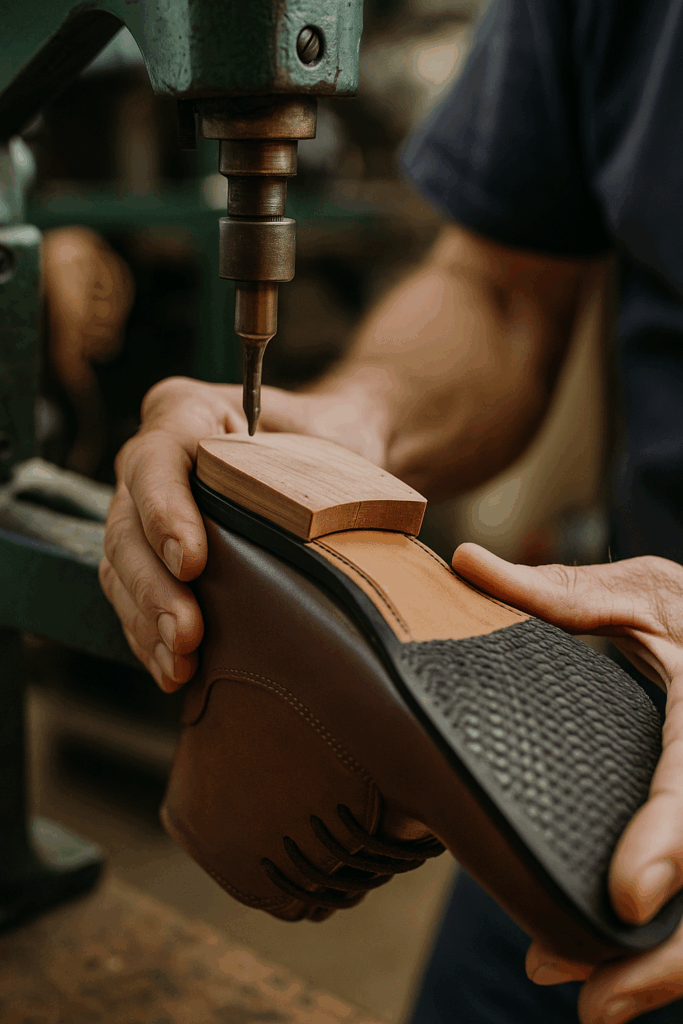
La dernière étape peut aussi être longue.
La chaussure est nettoyée et bichonnée. Le bichonnage consiste à cirer et à polir la chaussure. Certaines marques, surtout haut de gamme, mettent une attention particulière au cirage et polish. Ce bichonnage ne concerne que les chaussures en cuir.
La première de propreté, les lacets et les étiquettes de marque sont alors posés sur la chaussure.
Enfin, la chaussure est contrôlée puis est conditionnée pour la vente. Souvent la chaussure est mise dans un sac en tissu puis la paire dans une boite.
✏️ A noter : SCF fournit les lacets pour tous les types de chaussures.
Pour en finir avec la fabrication de chaussure
De nos jours, il existe 200 entreprises en France maitrisant le savoir-faire de la fabrication de chaussures.
C’est un savoir-faire d’exception et beaucoup d’entreprises forment elles-mêmes leurs salariés.
Fabriquer une chaussure est donc un processus complexe qui allie savoir-faire artisanal et, pour beaucoup d’entreprises, technologies industrielles.
✏️ A noter – Pour les accessoires, SCF continue de fournir lacets, tire-bottes et bordures aux usines française. Ses ventes excèdent largement le territoire, une forte part de l’activité de SCF étant exportées. MBB et la Manufacture de tressage récupèrent les fins de production pour les proposer après trie à la vente.